Case Study: How Well-Schooled Logistics Serve Education
Case Study: How Well-Schooled Logistics Serve Education
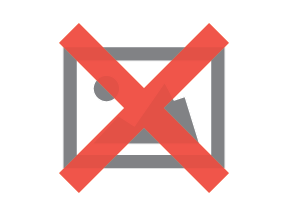
Over the course of 15 weeks in the summer of 2015, Atlas ® helmed the distribution of equipment and supplies at 44 education sites in 14 states. Following a process proven time and again, Atlas Logistics ® ensured the readiness of these facilities to help students learn and grow.
Major Roles
Client. The company that provides on-site education services.
Customer. The school or organization that contracts with the Client.
Site. The location where education takes place.
Vendors. The suppliers of goods to provision the Site.
Logistics Manager and Team. Atlas ® professionals who oversee inventory, provide essential communication up and down the supply chain, and intervene as needed to ensure the project’s timely completion.
Distribution Center. The secure, local warehouse where inventory is received, checked, and held for delivery.
Distribution Center Manager. The warehouse professional that receives and monitors inventory; assists in staging and loading goods for delivery.
Atlas Logistics ® Site Team. Skilled logistics hands that load and deliver goods to the Site; perform on-site services for unpacking, placement, debris removal, and reverse logistics if needed.
Receiving Site Team. Representatives of the Client who receive and inspect materials at the Site and oversee the inside placement.
***
At the Green Light
A project begins when the Client signs a contract with the Customer. The Logistics Team secures a suitable warehouse within proximity to the Site and gains agreement with the Warehouse Team on the scope of their work. The Warehouse Team understands the project’s just-in-time process and calendar frame (usually from 45 to 60 days).The Client places the order for materials via its purchasing management system. A typical project involves 20 different Vendors shipping 400 different SKUs. Both the Logistics Manager and Warehouse Team receive the inventory list from the Atlas Logistics ® system. The inventory list serves as the master list for receiving and checking off shipments as they come into the Warehouse. It details item descriptions, quantities, and Vendors. Each item carries a designated “interest area” that denotes its placement with similar items for delivery at the Site. For example, a basketball hoop is designated for the “sports & equipment” interest area.
The Distribution Center receives deliveries over the next four to six weeks. The Distribution Center Manager inspects products for signs of damage, continually updates the inventory list, and keeps products in a designated section of the warehouse for accountability and ready access. The inventory eventually totals about 2500 pounds. It includes items small and large, from boxes of pencils to palletized storage cabinets.
Countdown to Completion
Not only is timely delivery needed for the Site to be fully equipped on day one of the contract; the license to operate is also at stake. Two weeks before scheduled delivery to the Site, the Logistics Manager flags outstanding inventory items as overdue. The Atlas
® Project Manager contacts Vendors to confirm delivery and informs the Client of any potential need for alternate sources. This proactivity is a critical “fail safe” to ensure the order is delivered 100 percent complete. This Atlas
® Team monitors logistical flows with tenacity and responds swiftly to potential hiccups. The Project Manager occupies the command seat for information and communication, bringing practical, experienced decision-making to unexpected events.
On Site Services
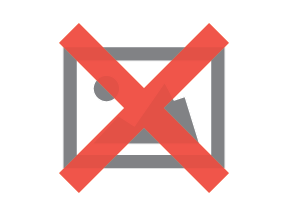